By now you’ve probably heard of Industry 4.0 and how it can help manufacturing processes. While going full-out digital and becoming a connected smart factory with state-of-the-art manufacturing equipment would present endless production opportunities, getting involved in such a large investment may not be the best choice for your company, especially with a slow return on investment. Considering a retrofit may be a much better solution for you.
One major reason why people decide against investing in wide sweeping, Industry 4.0 initiatives is because large transformations call for complex decisions on spending extensive amounts of capital upfront. What’s more, big investments often yield a slow ROI, causing people to wonder if the investment is worth the trouble. In comparison to implementing vast changes, retrofitting offers a nice alternative by being able to concentrate on something smaller and more specific that yields precise results. In effect, by exploring retrofitting options, people are able to get sample results of Industry 4.0 while not spending a fortune. What’s more, one smaller upgrade can lead to another, and another, which in turn allows plant managers and operators to slowly adapt their production floors to become more Industry 4.0- and smart factory-oriented through increments.
So what are good examples of when to retrofit and when not to retrofit?
Well, do you use your production floor to run a lot of jobs continuously where part changeovers happen frequently? Do you and your team spend more time than you would like programming and setting up for jobs and making frequent changeovers? If these circumstances present significant constraints with unwanted downtime, then a retrofit would be a good idea.
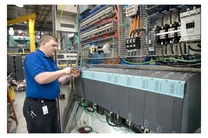
Well, do you use your production floor to run a lot of jobs continuously where part changeovers happen frequently? Do you and your team spend more time than you would like programming and setting up for jobs and making frequent changeovers? If these circumstances present significant constraints with unwanted downtime, then a retrofit would be a good idea.
If you need different types of machine heads for running different jobs, perhaps you can outfit one or two of your existing machines so they can be equipped with interchangeable machine heads. For instance if you need to have a combination of machine heads, such as straight heads for heavy-duty metal cutting; contour heads for profiling and curved cutting; and 90-degree heads for angled cutting, then retrofitting a machine so that it can use all three types interchangeably would be ideal. If you work with more than one type of axis, you could also further outfit your machinery so that the axes are interchangeable along with the heads.
While the above example of when to retrofit with metal cutting may be a given, there are other times when the idea of retrofitting sounds good in theory, although when you take into consideration the time and money needed to do so the idea may not pan out as perfectly as you would want. For instance, in a case where you are looking to get data information from an older piece of equipment for predictive analytics where the only place it can be seen is on a human-machine interface, having a custom-made device specially crafted for the sole purpose of being able to externally access data may be very costly. While connecting your equipment to IIoT systems has limitless potential, some older pieces of equipment may be very difficult to digitize as they were never meant to function in this way. In cases like these, the investment may not be worth what you’re trying to accomplish.
Let’s say you have a possible need for retrofitting but are unsure of the next steps to take. When considering doing a retrofit, you always want to create a specific goal that is as detailed as possible. For example, perhaps you and your staff are experiencing problems where production repeatedly gets bottlenecked in a certain area on your floor. What are your pain points? What could be done to improve the situation? This could be a good case for how retrofitting a piece of machinery could improve the situation.
In addition to pain points, other questions to ask yourself when contemplating a retrofit include the following:
- What are you trying to achieve?
- What is your current situation?
- What do you need in order to achieve the desired outcome?
After clearly assessing your needs, you can then form a business plan and even more detailed information on how a retrofit would be good for you and your company. How much time, money and products are lost by staff needing to clear bottlenecks that could be applied toward more seamless production? Any possible retrofit case needs to be backed by a careful cost analysis of how much money is being lost due to the current situation, how much the projected cost estimate would be to implement changes with a retrofit and how much money you would have to gain as an ROI over the course of one month, 6 months and a year after successful implementation.

Regardless of whether you plan to retrofit your equipment, go for a complete upgrade or keep your machinery as is, Mueller Electric is here to support you in your factory automation efforts, which is why we are pleased to announce that with the new additions to our molding line up Mueller Electric is now manufacturing instrumentation cables in Akron, OH
While our initiative to bring manufacturing back to the states has allowed us to replenish our stock levels, it has also provided us with the capabilities needed to manufacture standard, and custom, length 3, 4, 5 and 8-Pin M12 cables in-house, and deliver on competitive lead times on average of 5 DAYS or LESS! so you no longer have to wait for the cables that you need to keep your machines up and running.
With an extensive line of UL-listed M12 cables and custom-made solutions, Mueller Electric has the cables and solutions that are just right for you and your specific application.
Please feel free to contact us for a consultation and to learn how Mueller Electric can help you with your factory automation needs.
Coming Soon from Akron – M8 3 and 4-Pin and 7/8-16UN 2, 3, 4, 5, 6 and 8-Pin Cables
(All Lengths – All Configurations)
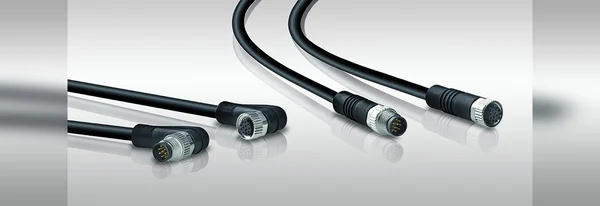